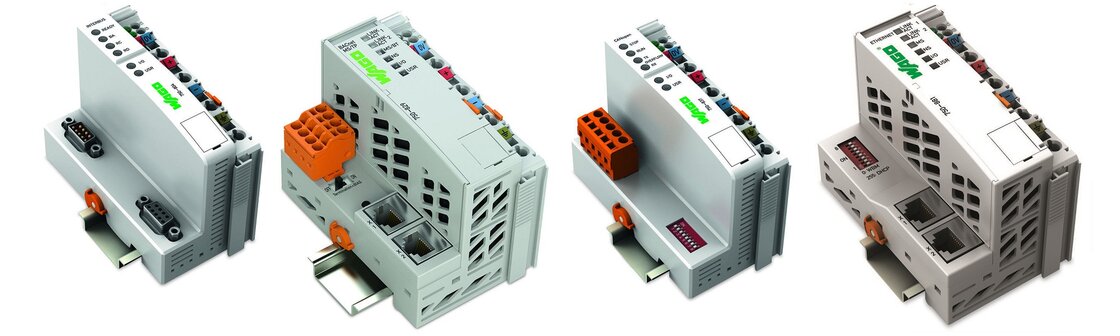
Брошури: WAGO PLC

Controller Interbus
The INTERBUS controller is an expansion for the WAGO-I/O-SYSTEM. This controller combines the WAGO fieldbus coupler for INTERBUS with the functionality of a PLC. Application programming is IEC 61131-3 compliant. The programmer can access all fieldbus and I/O data.
Features and applications:
-Decentralized control to optimize support for a PLC or PC
-Devide complex applications into individually testable units
-Programmable fault response in the event of fieldbus failure
-Signal pre-processing to reduce fieldbus transmissions
-Directly control peripheral equipment for faster system response times
-Stand-alone, compact controller
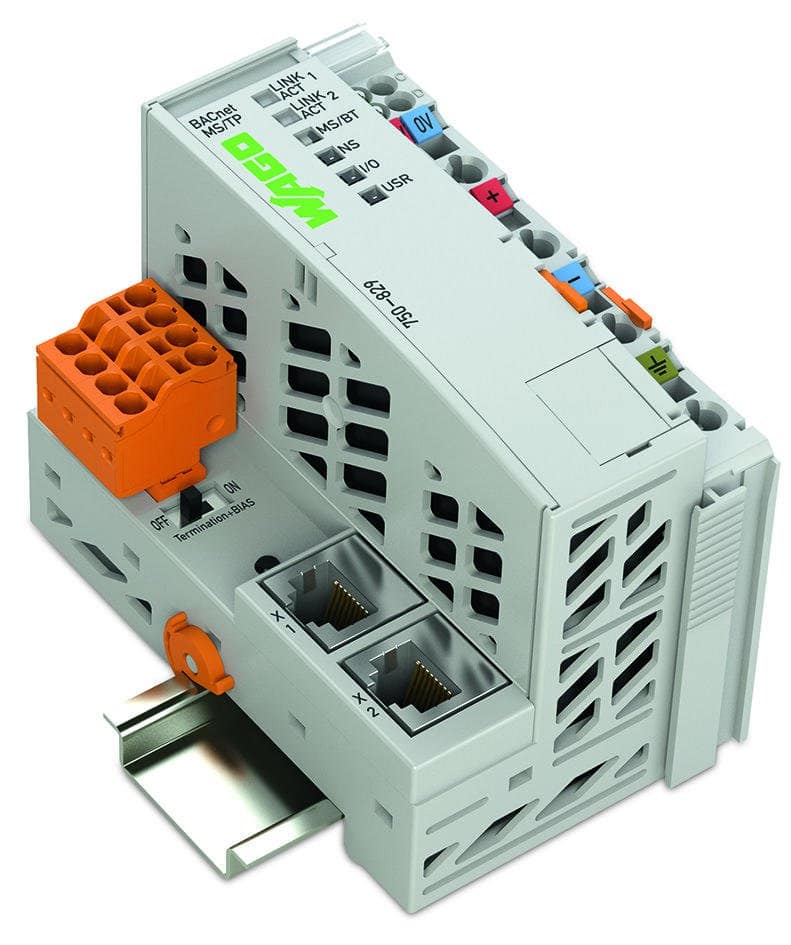
Controller BACnet MS/TP
The BACnet MS/TP Controller (750-829) connects the WAGO‐I/O-SYSTEM with the BACnet protocol. The 750-829 Controller supports the B‐BC BACnet device profile per DIN EN ISO 16484‐5. It communicates with other BACnet devices via BACnet MS/TP.
The controller provides the three following functionalities:
-Native server: For each channel, appropriate BACnet objects are generated automatically for the digital and analog I/O modules that are connected to the controller.
-Application server: Other supported BACnet objects can be created via IEC 61131‐3 programming environment and made available to a BACnet network.
-Application client: Using the client functionality, objects and their properties can be accessed by other BACnet devices

Controller PROFIBUS Slave
The PROFIBUS DP/V1 Controller combines control functionality, I/O interface and fieldbus in one device. Application programming is IEC 61131-3 compliant. The programmer can access all fieldbus and I/O data.
Features and applications:
-Decentralized control to optimize support for a PLC or PC
-Devide complex applications into individually testable units
-Programmable fault response in the event of fieldbus failure
-Signal pre-processing to reduce fieldbus transmissions
-Directly control peripheral equipment for faster system response times
-Stand-alone, compact controller
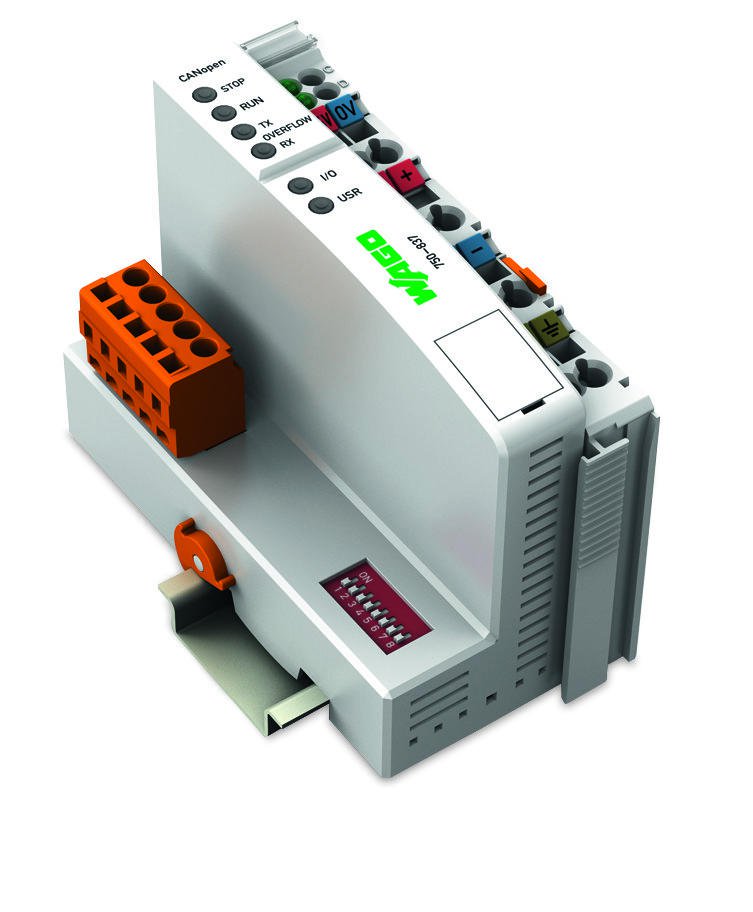
Controller CANopen; 128/64 KB Program/RAM; MCS
The PROFIBUS DP/V1 Controller combines control functionality, I/O interface and fieldbus in one device. Application programming is IEC 61131-3 compliant. The programmer can access all fieldbus and I/O data.
Features and applications:
-Decentralized control to optimize support for a PLC or PC
-Devide complex applications into individually testable units
-Programmable fault response in the event of fieldbus failure
-Signal pre-processing to reduce fieldbus transmissions
-Directly control peripheral equipment for faster system response times
-Stand-alone, compact controller
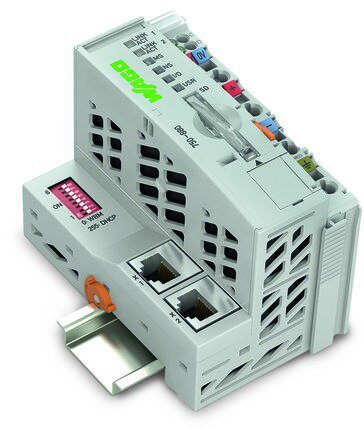
Controller ETHERNET; 3rd Generation; SD Card Slot
In conjunction with the WAGO-I/O-SYSTEM, the ETHERNET Controller can be used as a programmable controller within ETHERNET networks.
The controller supports all digital, analog and specialty modules found within the 750/753 Series, and is suitable for data rates of 10/100 Mbit/s.
Two ETHERNET interfaces and an integrated switch allow the fieldbus to be wired in a line topology. This eliminates additional network devices, such as switches or hubs. Both interfaces support Auto-Negotiation and Auto-MDI(X).
The DIP switch configures the last byte of the IP address and may be used for IP address assignment.
The controller supports both MODBUS/TCP and EtherNet/IP for use in industrial environments. It also supports a wide variety of standard ETHERNET protocols for easy integration into IT environments (e.g., HTTP, BootP, DHCP, DNS, SNTP, SNMP, FTP).
For use in telecontrol applications; the 750-880/025-001 and -002 Controllers support the IEC 60870-5-101/-103-104, IEC 61850-7, and IEC 61400-25 communication protocols.
An integrated Webserver provides user configuration options, while displaying PLC status information.
The IEC 61131-3 programmable controller is multitasking-capable and features a battery-backed RTC.
A data memory of 1 MB is available.
The 750-880 Controller is equipped with a removable memory card slot. A memory card can be used to transfer device parameters or files (e.g., boot files) from one controller to another. The memory card can be accessed via FTP and be used as an additional drive.
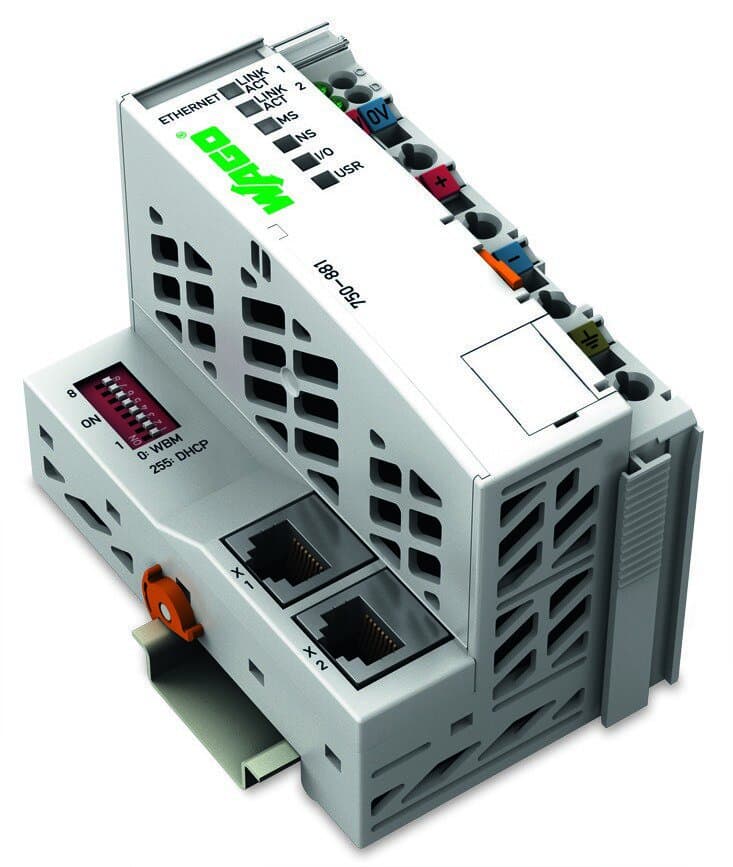
Controller ETHERNET; 3rd Generation
The ETHERNET Controller connects ETHERNET to the modular WAGO-I/O-SYSTEM.
The controller detects all connected I/O modules and creates a local process image. This process image may include a mixed arrangement of analog (word-by-word data transfer) and digital (bit-by-bit data transfer) modules.
Two ETHERNET interfaces and an integrated switch allow the fieldbus to be wired in a line topology. This eliminates additional network devices, such as switches or hubs. Both interfaces support Auto-Negotiation and Auto-MDI(X).
The DIP switch configures the last byte of the IP address and may be used for IP address assignment.
The controller is designed for fieldbus communication in both EtherNet/IP and MODBUS networks. It also supports a wide variety of standard ETHERNET protocols (e.g., HTTP, BootP, DHCP, DNS, SNTP, SNMP, FTP).
An integrated Webserver provides user configuration options, while displaying PLC status information.
The IEC 61131-3 programmable controller is multitasking-capable and features a battery-backed RTC.
750 XTR (наменето за во екстремни услови)
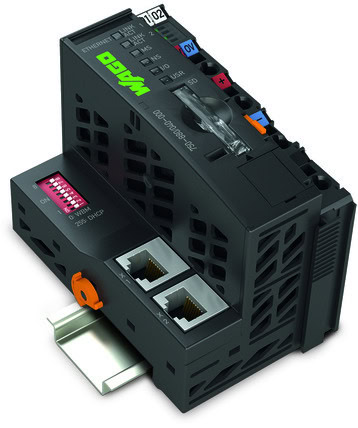
Controller ETHERNET; 3rd Generation; SD Card Slot; Extreme
In conjunction with the WAGO-I/O-SYSTEM, the ETHERNET Controller can be used as a programmable controller within ETHERNET networks.
The controller supports all digital, analog and specialty modules found within the 750/753 Series, and is suitable for data rates of 10/100 Mbit/s.
Two ETHERNET interfaces and an integrated switch allow the fieldbus to be wired in a line topology. This eliminates additional network devices, such as switches or hubs. Both interfaces support Auto-Negotiation and Auto-MDI(X).
The DIP switch configures the last byte of the IP address and may be used for IP address assignment.
The controller supports both MODBUS/TCP and EtherNet/IP for use in industrial environments. It also supports a wide variety of standard ETHERNET protocols for easy integration into IT environments (e.g., HTTP, BootP, DHCP, DNS, SNTP, SNMP, FTP).
For telecontrol applications, the 750-880/040-001 Controller supports the IEC 60870-5-101/-103-104, IEC 61850-7 and IEC 61400-25 communication protocols.
An integrated Webserver provides user configuration options, while displaying PLC status information.
The IEC 61131-3 programmable controller is multitasking-capable and features a battery-backed RTC.
A data memory of 1 MB is available.
The 750-880 Controller is equipped with a removable memory card slot. A memory card can be used to transfer device parameters or files (e.g., boot files) from one controller to another. The memory card can be accessed via FTP and be used as an additional drive.
The device is ideal for operation in harsh environments:
Extended temperature range
Greater immunity to impulse voltages and electromagnetic interference
Higher vibration and shock resistance
Derating: Total current for system supply: 1700 mA (ambient temperature (operation) < 60 °C), 1500 mA (ambient temperature (operation) 60–70 °C)
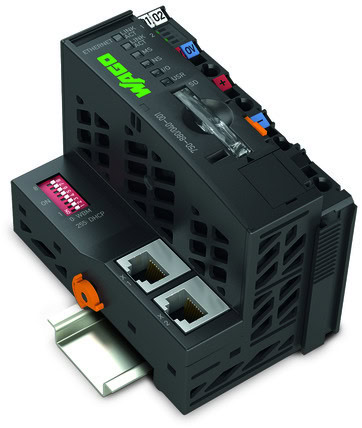
Controller ETHERNET; 3rd Generation; SD Card Slot; Telecontrol technology; Extreme
In conjunction with the WAGO-I/O-SYSTEM, the ETHERNET Controller can be used as a programmable controller within ETHERNET networks.
The controller supports all digital, analog and specialty modules found within the 750/753 Series, and is suitable for data rates of 10/100 Mbit/s.
Two ETHERNET interfaces and an integrated switch allow the fieldbus to be wired in a line topology. This eliminates additional network devices, such as switches or hubs. Both interfaces support Auto-Negotiation and Auto-MDI(X).
The DIP switch configures the last byte of the IP address and may be used for IP address assignment.
The controller supports both MODBUS/TCP and EtherNet/IP for use in industrial environments. It also supports a wide variety of standard ETHERNET protocols for easy integration into IT environments (e.g., HTTP, BootP, DHCP, DNS, SNTP, SNMP, FTP).
For telecontrol applications, the 750-880/040-001 Controller supports the IEC 60870-5-101/-103-104, IEC 61850-7 and IEC 61400-25 communication protocols.
An integrated Webserver provides user configuration options, while displaying PLC status information.
The IEC 61131-3 programmable controller is multitasking-capable and features a battery-backed RTC.
A data memory of 1 MB is available.
The 750-880 Controller is equipped with a removable memory card slot. A memory card can be used to transfer device parameters or files (e.g., boot files) from one controller to another. The memory card can be accessed via FTP and be used as an additional drive.
The device is ideal for operation in harsh environments:
Extended temperature range
Greater immunity to impulse voltages and electromagnetic interference
Higher vibration and shock resistance
Derating: Total current for system supply: 1700 mA (ambient temperature (operation) < 60 °C), 1500 mA (ambient temperature (operation) 60–70 °C)

Controller CANopen; 640/832 KB Program/RAM; D-Sub; Extreme
The CANopen Controller combines control functionality, I/O interface and fieldbus in one device.
Application programming is IEC 61131-3 compliant.
The programmer can access all fieldbus and I/O data.
Features and applications:
-Central control system is assisted by decentralized processing units
-Divide complex applications into individually testable units
-Programmable fault response in the event of fieldbus failure
-Signal pre-processing reduces fieldbus transmissions
-Peripheral equipment can be controlled directly, resulting in faster system response times (without any “detour” over the CANopen fieldbus system)
-Compact, self-sufficient controller
The device is ideal for operation in harsh environments:
Extended temperature range
Greater immunity to impulse voltages and electromagnetic interference
Higher vibration and shock resistance
Note: Configuration files required (EDS)!
The EDS files can be downloaded for free at www.wago.com.
Derating: Total current for system supply: 1650 mA (ambient temperature (operation) < 60 °C), 1250 mA (ambient temperature (operation) 60–70 °C)